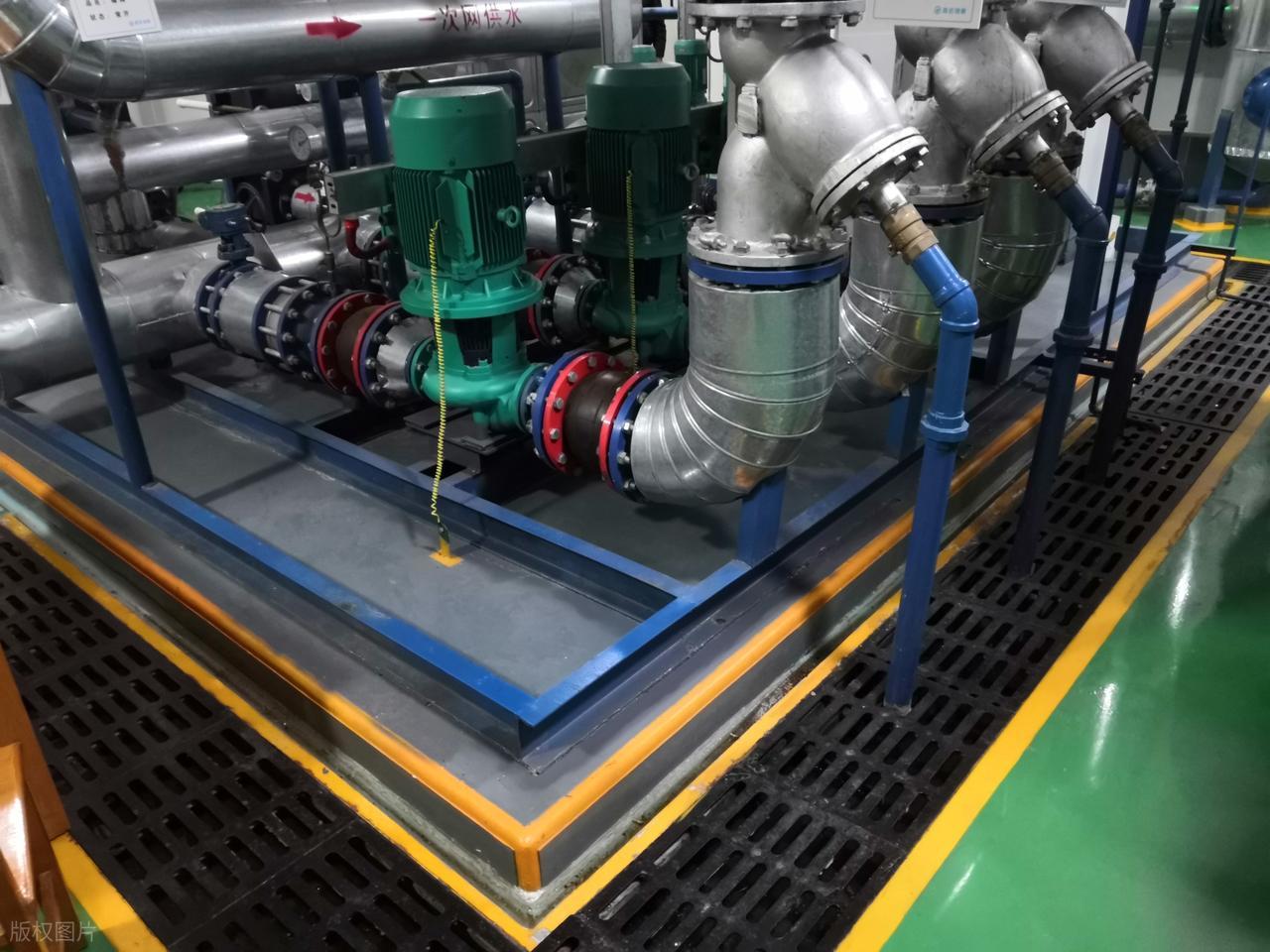
一、冷却循环水管道清洗注意事项
- 清洗前准备
- 制定详细清洗方案,包括清洗范围、药剂浓度、时间及安全措施。
- 检测水质,分析污垢成分(如碳酸钙、铁锈、生物粘泥),确定清洗方法(化学清洗、高压水射流清洗等)。
- 关闭相关阀门,隔离待清洗管道,排空系统内积水,确保无压力残留。
- 准备防护装备(安全帽、防护手套、护目镜)及应急物资(中和剂、吸液棉)。
- 清洗流程
- 预冲洗:启动循环水泵,用清水冲洗管道内壁,去除疏松污垢和悬浮物,持续至排水清澈。
- 杀菌剥离:加入高效粘泥剥离剂和渗透剂,循环 12-24 小时,杀灭微生物并剥离生物粘泥,排放污水后再次冲洗。
- 除垢清洗:根据管道材质选择化学清洗剂(如有机酸或无机酸),控制 pH 值和温度,循环清洗 2 次,每次 12 小时,确保水垢溶解并分散。
- 钝化处理:清洗后加入缓蚀剂或预膜剂,在金属表面形成保护膜,防止二次氧化。
- 最终冲洗:用清水置换至排水浊度<20ppm,检查管道内壁清洁度,清理 Y 型过滤器滤网。
- 清洗后维护
- 检查管道腐蚀情况,修补破损防腐层或更换受损管段。
- 恢复系统连接,启动试运行,监测压力、流量及水质指标(pH 值、电导率)。
- 记录清洗时间、药剂用量及效果,建立维护档案。
二、冷却塔维护注意事项
- 日常巡检
- 外观检查:每日检查塔体、支架、管道是否变形、泄漏,紧固松动螺栓,修复裂缝或密封胶脱落处。
- 运行状态:监测风机噪音、振动及皮带松紧度,调整扇叶角度至设计值,确保风量均匀。
- 水质管理:每周检测冷却水硬度、微生物含量,添加阻垢剂(如 ATMP、HEDP)和杀菌剂(如次氯酸钠、异噻唑啉酮),控制 pH 值在 7.5-9.5 之间。
- 填料清洁:每月冲洗填料表面污垢,防止堵塞影响换热效率,发现破损及时更换(通常 3-5 年更换一次)。
日常巡检 - 定期维护
- 季度维护:
- 深度清洗集水盘、喷淋系统及挡水帘,清除泥沙和藻类,确保排水畅通。
- 检查浮球补水装置功能,校准水位控制器,防止溢水或缺水。
- 测试电机绝缘性,补充轴承润滑油,更换磨损皮带。
- 年度维护:
- 全面拆检冷却塔内部,清洗管道及换热器,更换老化填料(高温环境下缩短至 4-6 年)。
- 检查塔体结构及防腐涂层,修复锈蚀或破损部位,重新涂刷防腐漆。
- 测试风机、水泵性能,校准自动补水装置,记录运行参数(进出口水温、流量)。
- 季度维护:
- 季节性维护
- 夏季:
- 增加水质检测频率(每周 2 次),加大杀菌灭藻剂投加量,防止微生物滋生。
- 检查冷却塔周边环境,清理杂物,确保通风良好,避免高温导致冷却效率下降。
- 冬季:
- 排空喷淋水和内部循环水,或添加乙二醇防冻液(冰点低于当地最低温),防止管道冻裂。
- 对碳钢管道采取防冻措施(如电伴热),避免排空后空气进入导致锈蚀。
循环水管道
- 夏季:
- 安全与环保要求
- 维护前切断电源并挂牌警示,禁止带电作业。
- 化学药剂储存于通风干燥处,分类存放,避免混用(如酸与碱性药剂)。
- 清洗废水需经中和处理,达到 GB50648-2011 标准后排放,禁止直接排入下水道。
- 高空作业时系好安全带,使用防滑踏板,避免踩踏填料。
三、常见问题处理
- 管道结垢
- 分析垢样成分,选择针对性清洗剂(如碳酸钙垢用盐酸,硅酸盐垢用氢氟酸)。
- 调整水质处理方案,增加阻垢剂投加量或更换高效药剂(如聚合物类阻垢剂)。
- 微生物滋生
- 交替使用氧化型(如二氧化氯)和非氧化型(如季铵盐)杀菌剂,避免微生物产生耐药性。
- 定期清洗冷却塔填料和集水盘,清除生物粘泥附着点。
- 设备腐蚀
- 检测水质腐蚀性离子(Cl⁻、SO₄²⁻),调整缓蚀剂配方(如锌盐与有机膦酸盐复配)。
- 检查管道防腐层完整性,修补破损处或采用阴极保护技术。
- 冷却效率下降
- 清洗填料和喷淋头,确保水分布均匀;检查风机风量,调整扇叶角度或更换老化皮带。
- 优化循环水量,避免流速过低导致污垢沉积。
四、应急预案
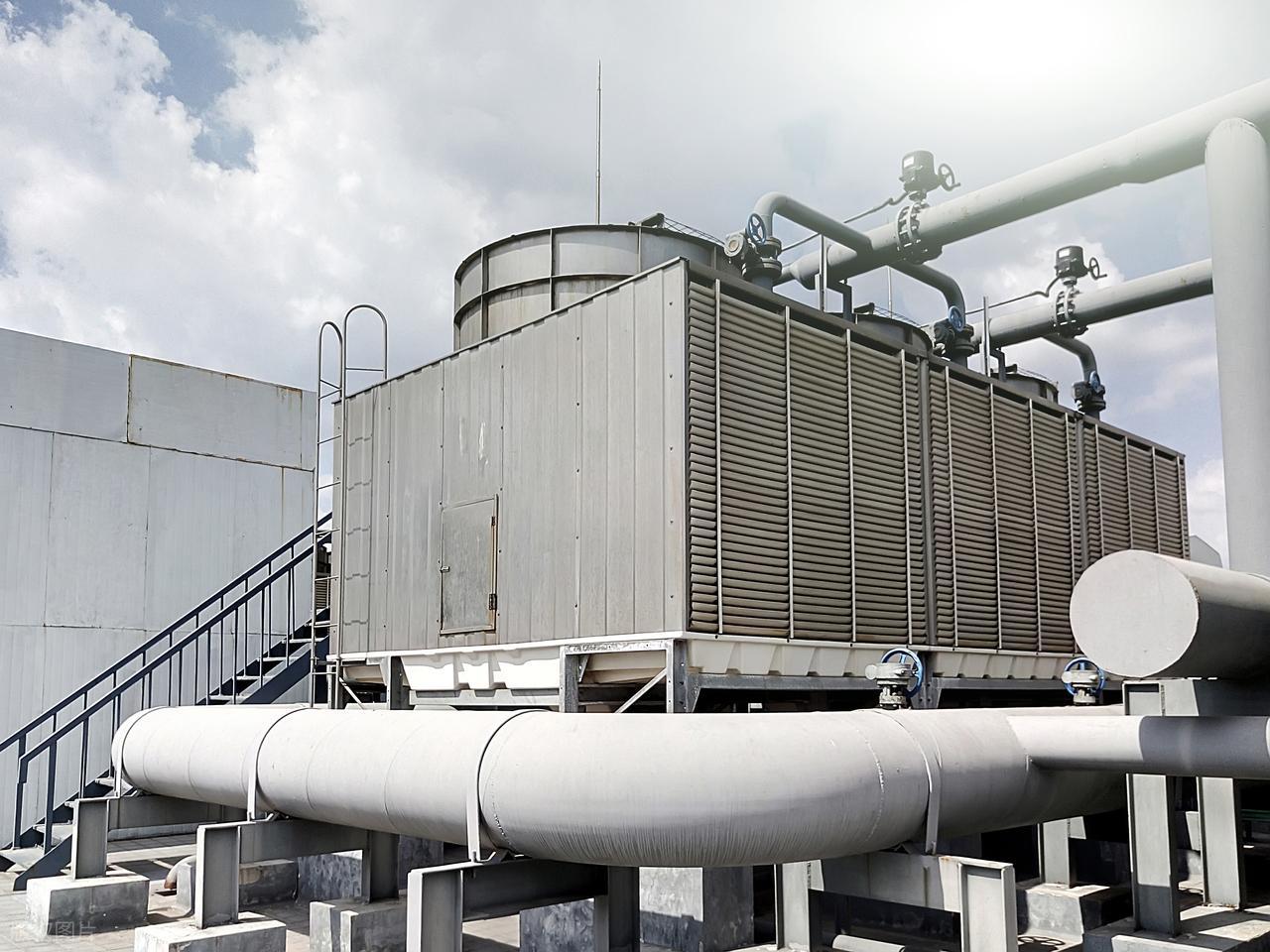
- 泄漏处理
- 立即关闭上下游阀门,停止系统运行,用吸液棉吸附泄漏液体,防止扩散。
- 分析泄漏原因(腐蚀、机械损伤),采用焊接、管卡或更换管段修复,修复后进行压力测试。
- 缺水报警
- 启动备用补水系统,检查水源供应及管道堵塞情况,必要时手动补水。
- 排查漏水点,修复后重新启动系统,监测水位及压力恢复正常。
- 设备故障
- 备用泵定期切换运行,确保主泵故障时能立即投入使用。
- 储备常用备件(如填料、皮带、阀门),缩短维修时间。
通过科学的维护计划和严格执行操作规范,可有效延长冷却循环水系统寿命,降低能耗,保障设备安全稳定运行。建议结合设备说明书及当地水质特点,制定个性化维护方案,并定期委托专业团队进行深度保养。